-
咨询服务CONSULTING SERVICE
-
精细加工FINE MACHINING
-
厂家直销DIRECT DEAL
-
大量现货LARGE STOCK
-
来图订制CUSTOM DRAWING
新闻中心
News Center
简述碳碳复合材料与其他材料的焊接研究
简述碳碳复合材料与其他材料的焊接研究
C/C复合材料是一种碳纤维增强的碳基体复合材料,具有密度小、比强度大、热膨胀系数低、耐高温、耐腐蚀、抗冲击和优良的摩擦性能等优点,而且在2 000 ℃下强度随温度的升高而升高,既可用作高温结构材料,又能用作功能材料,目前在航空航天、军工、医学及其它众多领域有着大量应用。在航空航天工业,C/C复合材料可用于导弹、火箭的部件,还可用于返回舱挡热板,飞机刹车盘及发动机的导管、喷嘴、叶片前缘等位置[1]。
C/C复合材料的制备成本较高,周期长且工序繁杂,因此在不影响结构使用性能的情况下将C/C复合材料和其它常用材料连接在一起可以降低成本、提高生产效率。但是C/C复合材料的焊接存在若干难题:①常用钎料对C/C复合材料基体的润湿性较差;②C/C复合材料的热膨胀系数与其它异种材料及钎料的热膨胀系数差异较大;③如何保证焊后接头还保持C/C复合材料的高温特性。
C/C复合材料的连接方式有机械连接、焊接、胶接等,文中仅针对C/C复合材料的焊接展开。由于C/C复合材料的熔点较高,难以采用熔焊的方法,目前其主要连接方式为钎焊和扩散焊,使用钎焊方法 焊接C/C复合材料简便、成本低、可以大量生产[2]。国内外对C/C复合材料与金属、非金属的焊接进行了大量研究,文中将从C/C复合材料之间以及C/C复合材料与钛及钛合金、高温合金、TiAl合金的焊接研究现状等方面进行论述。
1 C/C复合材料与C/C复合材料的焊接
1.1 C/C复合材料与C/C复合材料的钎焊
钎焊是目前C/C复合材料间最主要的焊接方式。易振华等人[3]通过试验证明含Ti质量分数为12%~16%的Ti-Cu合金钎料对C/C复合材料的润湿性最好;焊后Ti向C/C复合材料侧聚集并形成TiC,降低了界面张力,提高了钎料的润湿性。
陈波等人[4]研究了Pd-Ni基钎料对C/C复合材料的润湿性以及钎焊时的层间反应。采用四种Pd-Ni基钎料,分别为Pd-40Ni,PdNi-(4~11)Cr,PdNi-(12~25)Cr和 Ni-33Cr-24Pd-4Si,钎料均呈粉末状。对Ni-33Cr-24Pd-4Si钎料和C/C复合材料反应接头进行金相观察和能谱分析发现Cr和C/C复合材料反应形成Cr-C反应层,同时形成的还有Pd2Si,Pd3Si化合物,其余钎焊区域中富含Ni,缺少Pd。试验发现Pd-40Ni,PdNi-(4~11)Cr,PdNi-(12~25)Cr,Ni-33Cr-24Pd-4Si对C/C复合材料的润湿角分别为69°,75°,3°,2°,研究认为Cr含量的提高有助于Pd-Ni基钎料对C/C复合材料的润湿。
C/C复合材料钎焊构件通常在高温环境中使用,因此需要钎缝成分具有较高的熔点。M.Salvo等人[5]使用Si箔作为钎料钎焊C/C复合材料,钎焊温度为1 400 ℃,保温时间90 min。钎焊过程中Si与C反应形成SiC,在靠近钎料处形成Si/SiC层,在靠近母材处形成C/SiC层,获得的接头剪切强度为22 MPa。
Ti,Si及其合金均能用于C/C复合材料的钎焊,但接头抗氧化性较差且由于钎料基体热膨胀系数的差异易在接头处形成裂纹。玻璃钎料热膨胀系数低,部分玻璃钎料热膨胀系数非常接近C/C复合材料,但是玻璃钎料与C/C复合材料钎焊时易产生CO,CO2气体,在焊缝处形成气孔[2]。
C.lsola等人[1]使用SABB玻璃材料作为钎料钎焊C/C复合材料。SABB玻璃材料的成分为70.4SiO2-2.1Al2O3-17.5B2O3-10.0Ba0(质量分数,%)。因为C/C复合材料对大部分玻璃材料均不润湿,因此C/C复合材料表面需要经过SiC改性,SABB玻璃对SiC的润湿角为20°左右。将混合酒精与Si粉制成的Si浆涂抹在C/C复合材料表面,在惰性气体保护的环境下加热到Si熔点以上温度,此时会在C/C复合材料表面形成β-SiC层,在该研究中表面改性加热温度为1 550 ℃,保温1 h,升温速度为30 ℃/min,表面β-SiC层厚度小于150 μm。采用两种钎焊温度曲线,分别为1 200 ℃保温60 min升至1 300 ℃保温5 min以及直接1 300 ℃保温1 h,获得的接头室温剪切强度均达到30 MPa。
根据目前的研究现状,C/C复合材料之间的钎焊可以采用以下主要方式。
(1)通过改变钎料中活性元素(Ti,Cr等)的含量提高钎料对C/C复合材料母材的润湿性。钎焊时,这些活性元素向钎料与母材连接界面聚集,产生化合物形成接头。采取这种钎焊方式会面临钎料与母材热膨胀系数差异较大引发裂纹的问题。
(2)使用Si或Mg2Si化合物钎料进行钎焊。该方式主要通过反应而非润湿形成接头,其优点在于钎缝成分性能与母材接近,缺点在于反应过程中易在钎缝附近形成气孔,影响钎缝强度。
(3)通过在C/C复合材料待焊面进行表面处理,如涂覆、烧结、沉积、打孔等,在表面形成一层焊接性更好的过渡层或者增加钎焊面积,可提高钎料对母材的润湿作用,同时能缓解因钎料母材热膨胀系数的差异产生裂纹。
1.2 C/C复合材料与C/C复合材料的其它焊接方式
扩散焊也是C/C复合材料焊接常用的方式。相对于钎焊工艺,扩散焊接时,中间层材料与母材元素之间的互扩散更加剧烈。C/C复合材料间的扩散连接时可在母材表面涂覆、沉积Mn粉等金属粉末,一定温度下形成碳化物连接层,继续升温碳化物分解,分解出的金属元素蒸发从而生成连续的石墨连接层。硼和硼化物常被用于C/C复合材料的扩散焊,焊接时硼与碳能够完全反应形成B4C,获得的接头在高温环境下的剪切强度与C/C复合材料固有层间强度相当[2]。
王杰等人[6]使用Ti-Ni-Si合金作为中间层真空扩散焊接C/C复合材料。试验证明最佳的焊接参数为加热温度1 150 ℃,加压30 MPa,保温45 min,在该参数下获得的焊接接头平均剪切强度达到23.58 MPa。结果表明在连接区域发生了元素的互扩散和化学反应,该区域化合物包括Ni4Si7Ti4,TiSi2, SiC和TiC等。在接头处有三种裂纹形式,这些裂纹容易在层间、界面和C/C复合材料基体上产生。对接头进行热疲劳试验发现接头的剪切强度在经过5次热循环之后急剧下降。分析由于Ti合金与C/C复合材料的热膨胀系数差距较大,因此在热循环下钎料母材膨胀程度不同产生位错,从而易于形成裂纹。
自蔓延连接(Combustion Joining,简称CJ)也被用做C/C复合材料的连接方法。它将中间层粉末或多层夹层自蔓延高温合成反应产生的热量做为热源,是C/C复合材料的连接中一种节能的方法。此连接方法类似于压力焊,例如将基体与连接材料放置在两个铜电极之间通过加压加热使材料连接。该方法目前使用的夹层有Ti-C,Si-C,Ni+Ti/Ni+Al等 [7]。
Lin Ya-Cheng 等人[8]通过自蔓延连接对C/C复合材料进行连接。中间层材料采用钛合金和Ni/Al粉末的混合物,连接方式如图1所示。在连接前将工件预热到630 K,连接初始压力为4 MPa,最终压力为20~40 MPa,应用的电流为200~400 A,持续时间5 s。经过热成像分析,在0.8~0.9 s的时候工件的温度达到最高,达1 500 K。焊后工件连接处产生了75~100 μm、无气孔但有大裂纹的连接层,该连接层由NiAl和TiC组成。
扩散连接是C/C复合材料间主要的焊接方式之一。C/C复合材料间的扩散连接与钎焊的不同点在于C/C复合材料间的扩散连接更注重于通过高温高压下的反应形成稳定的中间连接层,而钎焊工艺则注重通过改变钎料活性元素的含量、母材表面改性等措施提高钎料对母材的润湿性。
C/C复合材料的扩散连接获得的连接接头高温性能稳定,但其通常采用高温高压环境下析出中间层杂质相的方式易在连接层界面产生缺陷。
自蔓延连接这种新型的连接方式获得的焊接接头能满足一定的强度要求,但这种方式易面临焊后中间层裂纹的问题,该问题需在今后的研究中加以克服。
2. C/C复合材料与钛及钛合金的焊接
钛合金比强度高、抗腐蚀性能好、综合力学性能优异,是目前航空航天领域的明星材料。将钛合金与具有优异高温性能的C/C复合材料连接起来能够获得质量轻、高温性能好、能够满足一定结构强度要求的连接件,在航空航天等领域有着广泛的应用前景。银基、钛基钎料是C/C复合材料与钛合金钎焊常用的钎料。M.Singh等人[15]采用三种钎料钎焊C/C复合材料与纯钛,三种钎料分别为Cu-ABA,TiCuNi和TiCuSi,均呈箔状,厚度约为50 μm。分析发现,在钎焊过程中溶质的再分配和扩散导致的冶金结合保证了钎料对基体的润湿性。C/C复合材料中的C纤维束的取向影响了接头的性能,采用Cu-ABA钎料能够获得最佳的接头性能;C纤维束的方向垂直于Ti管轴获得的接头承载能力最高,C纤维束的方向平行于Ti管轴获得的接头承载能力最低。
郭伟等人[16]对C/C复合材料和TC4钛合金的钎焊进行了研究,采用的钎料为AgCu钎料(72Ag-28Cu,质量分数,%)。钎焊温度820~940 ℃,保温3~30 min。焊接时TC4钛合金中的Ti扩散到钎料和C/C复合材料中,提高了钎料对C/C复合材料的润湿性并且和钎料、母材发生化学反应。试验证明,可以通过AgCu钎料钎焊C/C复合材料和TC4钛合金,接头界面为TC4/Ti2Cu+Ti(s.s)/Ti2Cu/TiCu/Ag(s.s)+Ti3Cu4/TiC/C/C复合材料,获得的接头剪切强度在880 ℃时可保持33 MPa达10 min。
秦优琼等人[17]采用Ti-Zr-Cu-Ni非晶态合金钎料钎焊C/C复合材料和TC4钛合金。在C/C复合材料、TC4钛合金与箔状钛基钎料之间分别加入一层Cu中间层和一层Mo中间层,这样一方面可避免钎料与TC4钛合金母材形成大量钛铜、钛镍等脆性化合物,另一方面可缓解由于母材与钎料热膨胀系数差异在接头处产生的残余应力。结果证明,这种方法能用于C/C复合材料和TC4钛合金的钎焊,且随着钎焊温度的增加和保温时间的增长,Cu和Mo中间层的溶解加剧,形成连续、厚度较大的反应层。
由于银基、钛基钎料对C/C复合材料的润湿性较差,需要提高温度来改善钎料对母材的润湿性,当钎焊温度超过了钛合金的相变温度时,会导致整体结构的韧塑性下降。因此,焊前对C/C复合材料进行表面处理,在C/C复合材料表面添加一些与钎料润湿性好的材料,可以降低钎焊温度,提高接头的性能[18]。李争显等人[19]在TC4钛合金表面沉积一层镍层,厚度为3 μm,采用真空钎焊焊接TC4钛合金与C/C复合材料,钎料采用银基钎料和镍基钎料,钎焊温度为800~850 ℃,保温时间15 min,得到的钎焊接头室温剪切强度达到48 MPa。
综上所述,目前钎焊是C/C复合材料与钛合金焊接的主要手段,银基钎料、钛基钎料等均可用于C/C复合材料与钛合金的钎焊。
钛合金与C/C复合材料钎焊的优势在于Ti本身对C/C复合材料的润湿性比较好,但是钎焊温度超过钛合金相变温度时会降低钎焊接头的性能。通过在母材表面沉积镍层等处理方式可以降低钎焊温度,保证钎焊温度不超过钛合金的相变温度。
钛合金与C/C复合材料的钎焊主要依靠钎料与母材元素的润湿与扩散,因此采用合理钎焊温度和保温时间来保证钎料母材的充分反应,避免产生过量金属间化合物。
3. C/C复合材料与TiAl合金的焊接
TiAl合金因其低密度、高比强度、高温抗蠕变性能好,在飞行器涡轮发动机组件等部位的应用取得了优异的效果。使用包含50%(质量分数,%)的C/C复合材料的C/C-TiAl连接材料能节省27%的质量,从而提高发动机的推重比。C/C复合材料与TiAl合金的连接可提高高温构件的工作温度,扩展应用范围[20]。曹健等人[21]利用自蔓延连接的方法对C/C复合材料和TiAl合金(Ti-46Al-2Cr-2Nb,原子分数,%)进行连接,采用Ag-Cu-Ti钎料(Ag-26.4Cu-4.5Ti,质量分数,%)与Ti-Al-C夹层。在连接过程中,将近8 s时工件中心峰值温度达到1 943 ℃,靠近Ti-Al-C夹层附近温度在近20 s时也达到1 644 ℃,远高于Ag-Cu-Ti钎料的熔点。改变Ti-Al-C夹层的厚度发现试样的抗剪切强度随夹层厚度增加先提高后降低,在夹层厚度为500 μm时达到最大,此时工件的剪切强度为17.6 MPa,通过金相观察结果发现靠近C/C复合材料侧有大量TiC化合物,靠近TiAl合金侧则含有大量Ti-Al-Cu,中间夹层附近则以TiAl3和TiC居多。
王厚勤等人[22]使用Ag-Cu-Ti钎料钎焊C/C复合材料与TiAl合金。使用的TiAl合金为Ti-46Al-2Cr-2Nb,钎料为Ag-26.7Cu-4.6Ti(质量分数,%),箔状,厚度为50 μm。试验前用针在C/C复合材料表面刺出一些直径为0.8 mm、深度为1~3 mm的小孔。试验证明,Ag和Ti之间的互斥对接头的微观组织有明显的影响,钎焊温度1 193 K,保温10 min时,得到的接头典型结构为TiAl/Ti3Al+AlCuTi/AlCu2Ti/Ag(s.s)/TiC/CC。当连接温度低于1 213 K时,接头处出现了银基固溶体的等温线凝固,此时在界面处出现层结构,等温线凝固有助于降低Ti在C/C复合材料表面的聚集;层结构在连接温度达到1 213 K时被破坏,这会降低接头的强度。C/C表面被刺破的小孔导致的渗透层可显著强化接头,提高接头的抗冲击能力。
目前国内展开了一些C/C复合材料与TiAl合金的焊接研究。自蔓延连接能用于C/C复合材料与TiAl合金的焊接,焊接时为保证接头的抗剪切强度需要合理控制中间层的厚度。C/C复合材料与TiAl合金钎焊时可通过对C/C复合材料进行表面打孔处理提高钎焊接头的强度。
4. C/C复合材料与高温合金的焊接
高温合金抗氧化性能好,抗热腐蚀性能优异,工作温度高,组织稳定且有害相少,能在较高温度与应力的环境下工作,它广泛地应用于制造航空发动机、各类燃气轮机的最热端部件,如涡轮部分的工作叶片、涡轮盘、燃烧室等部件[9]。C/C复合材料在室温时强度较低且制备周期长、成本高,而C/C复合材料与镍基高温合金连接后质量轻、承载能力高、高温寿命长。镍基钎料是C/C复合材料与镍基高温合金钎焊的最常用钎料。吴永智等人[10]使用BNi68CrWB钎料钎焊C/C复合材料和GH600高温合金。钎焊温度为1 150 ~1 200 ℃,保温10 min。试验表明,Ni不与C形成化合物,该钎焊温度也达不到Si与C的反应温度。接头处主要是Ni与Si,Cr与C发生反应形成化合物促进钎料与母材的润湿。焊后接头室温剪切强度为50 MPa,在700 ℃下的剪切强度为22 MPa。接头断裂破坏的主要因素为各部分材料热膨胀系数差距较大导致的受热位错。在钎焊过程中,B由于无法向C/C复合材料扩散,反而与W在钎料母材界面处形成大块不均匀的WB化合物也是导致断裂的原因。接头的高温剪切强度受C/C复合材料氧化的影响而下降。
C/C复合材料与高温合金不互溶,热膨胀系数差异大,因此直接将C/C复合材料与高温合金连接在一起效果并不理想。对C/C复合材料进行表面处理或者在钎料中添加一些促进润湿的物质能够改善钎焊接头的强度。
郭领军等人[11] 使用Ni-Ti粉末作为连接材料真空扩散连接C/C复合材料和GH3128高温合金,一组C/C复合材料表面不作处理,一组C/C复合材料表面涂敷SiC涂层。扩散焊加热温度为1 050~1 250 ℃,加压8~20 MPa,保温60 min。结果发现未涂敷SiC涂层时,所获得的接头抗剪强度几乎为0;而涂敷SiC涂层时,在不同的加热温度下,接头的剪切强度差距较大,在加热温度为1 170 ℃时可以获得剪切强度为23 MPa的接头,而在1 130~1 150 ℃时,接头有明显的裂纹缺陷,因此剪切强度较低。经过分析,SiC涂层一方面能够增强Ti,Ni等元素对C/C复合材料的润湿性,另一方面可缓解因C/C复合材料与GH3128高温合金热膨胀系数不同产生的热应力。
田晓羽等人[12]通过添加TiH2的BNi2粉状钎料钎焊C/C复合材料和GH99镍基高温合金,钎焊温度为1 170 ℃,保温时间为1 h,分别采用含TiH2量为1%,3%,8%的钎料进行钎焊,结果发现钎料中含TiH2量为3%时获得的接头性能最好。原因在于TiH2中的Ti能够促进C/C复合材料向钎缝中的扩散,产生弥散的MC颗粒,降低C/C复合材料基体与钎缝的不匹配程度,缓
解残余应力;但钎料中TiH2含量过多时,钎缝中会产生大量的片状TiC,降低接头的塑性变形能力。采用含3% TiH2的BNi2钎料进行钎焊时获得的接头抗剪强度在室温为40 MPa,在800 ℃可达19 MPa,明显高于仅用BNi2钎料进行钎焊获得的接头。
张鑫等人[13]使用BNi5钎料真空钎焊C/C复合材料与镍基高温合金GH3044,钎料呈粉状,钎焊温度为1 180 ℃,保温30 min。进行两组试验,其中一组C/C复合材料表面SiC改性,另一组复合材料表面不作处理。结果表明,使用BNi5钎料可以成功焊接经过表面SiC改性的C/C复合材料与镍基高温合金GH3044,而焊接未经表面改性的C/C复合材料时在C/C复合材料与钎料界面会产生裂纹。经过分析,一方面SiC涂层有效的减缓了C/C复合材料与镍基高温合金因为热膨胀系数相差较大产生的热应力;另一方面,钎料与表面改性的C/C复合材料反应形成的中间层具有一定的韧塑性致使断裂发生在C/C复合材料一侧。获得的接头常温下剪切强度达到35.08 MPa,接头界面为C/C/Ni(s.s)+Cr7C3+Ni3Si/Ni(s.s)+Cr3C2+Ni3Si/Ni(s.s)+Cr3C2+MC+Ni3Si/Ni3Si+MC+Ni(s.s)/GH3044,s.s表示固溶体。
沈元勋等人[14]通过Ag-Cu钎料钎焊C/C复合材料和镍基高温合金,镍基高温合金的成分为Ni-20Cr-8W-7.5Mo-2Fe-0.6Al-0.5Ti (质量分数,%)。Al2O3夹层的厚度为2 mm,钎料为箔状Ag-28Cu,厚度为250 μm。进行三组试验,第一组不使用Al2O3夹层直接钎焊;第二组在两层钎料中夹持Al2O4016层;第三组不仅在两层钎料中夹持Al2O4016层而且对C/C复合材料表面进行激光打孔处理。钎焊温度为910 ℃,保温10 min。焊后第一组接头弯曲强度只有16 MPa,第二组接头弯曲强度为33 MPa,第三组接头弯曲强度为73 MPa,这说明添加Al2O3夹层,对C/C复合材料表面进行打孔处理均能提高钎焊接头的弯曲强度。经过分析,不加Al2O3夹层的焊后接头由于残余应力大导致弯曲强度非常低,添加Al2O3夹层能够获得结合良好且韧性高的接头的原因在于Al2O3夹层能够有效防止Ni和Ti的扩散及反应,降低接头的残余应力;对C/C复合材料表面进行激光打孔,使表面呈波浪形能够增大连接面积,降低残余应力,同时在母材表面的小孔处钎焊形成的针状物提高了对C/C复合材料的连接强度。
目前国内外进行了大量C/C复合材料与镍基高温合金的钎焊研究。C/C复合材料与镍基高温合金钎焊的主要问题有:①镍对C/C复合材料的润湿性差;②镍基钎料与C/C复合材料热膨胀系数差异较大,易引发连接界面处的裂纹。
针对上述问题,目前通常采用的主要措施为对母材进行表面改性,进行SiC表面改性等方式可以促进钎料与母材的润湿,同时可以缓解C/C复合材料与高温合金因热膨胀差异较大产生的热应力。另外通过优化钎料添加成分或使用过渡层的方式能够有效缓解焊接残余应力。
5 结 论
由于C/C复合材料熔点高,难以采用熔焊工艺,因此主要采用钎焊和扩散焊方法进行焊接。C/C复合材料钎焊与扩散焊时面临的主要问题有:①常用钎料对C/C复合材料的润湿性不好;②C/C复合材料的热膨胀系数很低,与大部分钎料的热膨胀系数差距大,高温下焊缝内会形成较大的热应力而开裂;③为了充分发挥C/C复合材料的高温性能优势,通常要求其焊缝具有良好的高温性能。为了解决上述问题,目前国内外研究主要采取了以下措施:①对C/C复合材料表面进行处理,如涂覆、烧结、打孔、沉积SiC等材料,可以提高母材与钎料润湿性、在接头界面形成过渡层防止热膨胀不均产生裂纹等;②在钎料中添加一些活性元素或化合物,这些活性元素化合物能够促进C/C复合材料向钎缝中的扩散,产生弥散颗粒,降低C/C复合材料基体与钎缝的不匹配程度,缓解残余应力;③改变钎料中活性元素的含量以提高钎料对C/C复合材料母材的润湿性;④C/C复合材料的扩散焊时可在母材与中间层之间夹持过渡层,缓解母材与钎缝的热膨胀程度差异。
未来C/C复合材料连接技术的发展将会得到各国高精尖产业的更多重视。现阶段,C/C复合材料与钛合金、高温合金等的焊接已经成功实现。如何有效解决目前C/C复合材料焊接常见的问题(如接头产生裂纹、接头高温性能差等)也是未来研究的热点。如同目前自蔓延连接这类新型方式的应用,今后必然将会产生更多新型的方法用于推进C/C复合材料连接技术的进步。更多碳碳复合材料信息可查看http://www.tqtf008.top
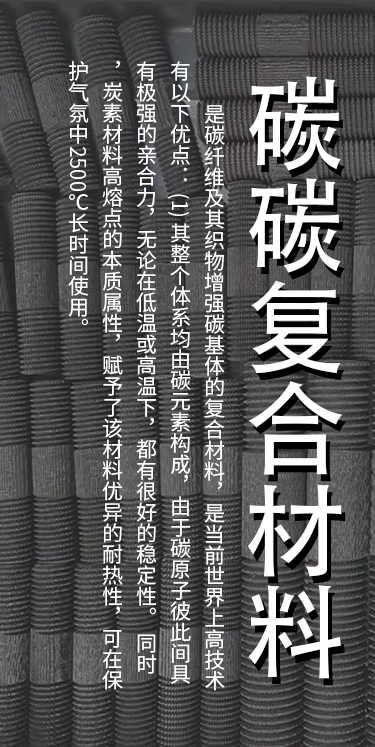
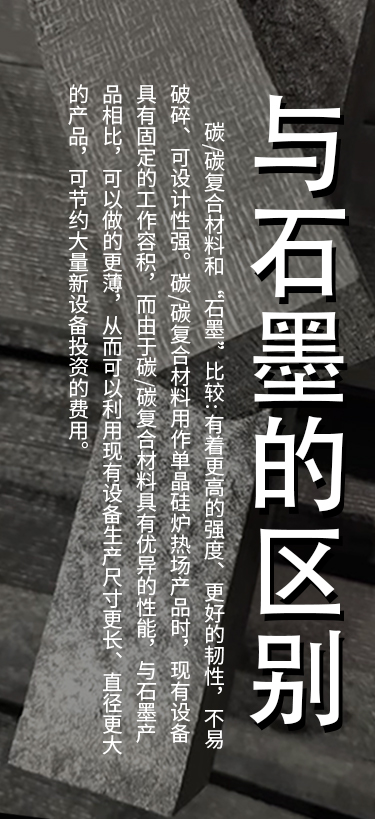
相关推荐
您的更多选择