-
咨询服务CONSULTING SERVICE
-
精细加工FINE MACHINING
-
厂家直销DIRECT DEAL
-
大量现货LARGE STOCK
-
来图订制CUSTOM DRAWING
简述一下碳碳复合材料致密化抗氧工艺
碳/ 碳致密化工艺过程就是基体碳形成的过程, 实质是用高质量的碳填满碳纤维周围的空隙, 以获得结构、 性能优良的碳/ 碳复合材料。最常用的有两种制做工艺: 液相浸渍法和化学气相沉积法。
1)液相浸渍法 液相浸债工艺是制造碳/ 碳的一种主要工艺。 按形成基体的浸渍剂, 可分为树脂浸渍、 沥青浸渍及沥青树脂混浸工艺; 按浸渍压力, 可分为低压、 中压和高压浸渍工艺。 通常可用做先驱体的有热固性树脂, 例如: 酚醛树脂和呋喃树脂以及煤焦油沥青和石油沥青。
浸渍用基体先驱体的选择 在选择基体的先驱体时, 应考虑下列特性: 黏度、产谈率、 焦炭的微观结构和晶体结构。 这些特性都与碳/ 碳复合材料制造过程中的时间-温度-压力关系有关。 绝大多数热固性树脂在较低温度(低于 250oC)下聚合成高度交联的、 不熔的非晶固体。 热解时形成玻璃态碳, 即使在 3000 oC 时也不能转变成石墨, 产碳率为 50%—56%, 低于煤焦油沥青。 加压碳化并不使碳收率增加, 密度也较小(小于 1,5g/ cm3)。 酚醛树脂的收缩率可达 20%, 这样大的收缩率将严重影响二向增强的碳/ 碳复合材料的性能。收缩对多向复合材料性能的影响比二向复合材料小。 预加张力及先在 400—600oC 范围内碳化, 然后再石墨化都有助于转变成石墨结构。 沥青是热塑性的, 软化点约为 400oC, 用它作为基体的先驱体可归纳成以下要点: 0.1MPa 下的碳收率约为 50%; 在大于或等于 10 MPa压力下碳化, 有些沥青的碳收率可高达 90%; 焦炭结构为石墨态, 密度约为 2g/ cm3, 碳化时加压将影响焦炭的微观结构。
低压过程 预制件的树脂浸渍通常将领制体置于浸渍罐中, 在温度为 50 oC 左右的真空下进行浸渍, 有时为了保证树脂渗入所有孔隙也施加一定的压力, 浸渍压力逐次增加至 3~5MPa, 以保证织物孔隙被浸透。 浸渍后, 将样品故入固化罐中进行加压固化, 以抑制树脂从织物中流出。采用酚醛树脂时固化压力为l MPa 左右,升温速度为 5~10oC/h, 固化温度为 140~170oC, 保温 2h; 然后, 再将样品放入碳化炉中,在氮气或氩气保护下, 进行碳化的温度范围为 650~1100oC, 升温速度控制在 10~30oC/h,最终碳化温度为 1000 oC, 保温 1h。
沥青浸渍工艺常常采用煤沥青或石油沥青作为浸渍剂, 先进行真空浸渍, 然后加压浸渍。 将装有织物预制体的容器故人真空罐中抽真空, 同时将沥青放人熔化罐中抽真空并加热到 250oC, 使沥青融化, 强度变小; 然后将熔化沥青从熔化罐中注入盛有预制体的容器中, 使沥青浸没预制体. 待样品容器冷却后, 移人加压浸渍罐中, 升温到 250℃进行加压涅渍, 使沥青进一步浸入预制体的内部空隙中, 随后升温至600~700oC 进行加压碳化。
为了使碳/ 碳具有良好的微观结构和性能, 在沥青碳化时要严格控制沥青中间相的生长过程, 在中间相转变温度(430~460℃). 控制中间相小球生长、 合并和长大。 在碳化过程中树脂热解, 形成碳残留物, 发生质量损失和尺寸变化, 同时在样品中留下空隙。 因此, 浸渍——热处理需要循环重复多次, 直到得到一定密度的复合材料为止。 低压过程中制得的碳/ 碳复合材料的密度为 1.6~1.65g/ cm3。, 孔隙率为 8%—10%。
高压过程 先用真空——压力浸渍方法对纤维预制体浸渍沥青, 在常压下碳化, 这时织物被浸埋在沥青碳中, 加工以后取出已硬化的制品, 把它放入一个薄壁不锈钢容器(称为“包套” )中, 周围填充好沥青, 并将包套袖真空焊封起来; 然后将包套放进热等静压机中慢慢加热, 温度可达 600~700oC, 同时施加 7~100 MPa 的压力。 经过高压浸渍碳化之后, 将包套解剖, 取出制品, 进行粗加工. 去除表层; 最后在 2500~2700oC 的温度和氩气保护下进行石墨化处理。
上 6 碳/ 碳复台材料的氧化保护 碳/ 碳复合材料具有优异的高温性能, 当工作温度超过 2000oC 时, 仍能保持其强度, 它是理想的耐高温工程结构材料, 已在航空航天及军事领域得到广泛应用。 但是, 在有氧存在的气氛下, 碳/ 碳复合材料在 400oC 以上就开始氧化。
碳/ 碳复合材料的氧化敏感性限制了它的扩大应用。 解决碳/ 碳复合材料高温抗氧化的途径主要是, 采用在碳/ 碳复合材料表面施加抗氧化涂层, 使 C 与 O2 隔开, 保护碳/ 碳复合材料不被氧化。 另一个解决高温抗氧化的途径是, 在制备碳/ 碳复合材料时, 在基体中预先包含有氧化抑制剂。
1)抗氧化涂层法 在碳/ 碳复合材料的表面进行耐高温氧化材料的徐层, 阻止与碳/ 碳复合材料的接触, 这是一种十分有效地提高复合材料抗氧化能力的方法。
一般而言, 只有熔点高、 耐氧化的陶瓷材料才能作为碳/ 碳复合材料的防氧化涂层材料。 通常, 在碳/ 碳复合材料表面形成涂层的方法有两种: 化学气相沉积法和固态扩散渗透法。 防氧化涂层必须具有以下特性: 与碳/ 碳复合材料有适当的黏附性, 既不脱粘, 又不会过分渗透到复合材料的表面; 与碳/ 碳复合材料有适当的热膨胀匹配, 以避免涂覆和使用时因热循环造成的热应力引起涂层的剥落; 低的氧扩散渗透率, 即具有较高的阻氧能力, 在高温氧化环境中氧延缓通过涂层与碳/ 碳复合材料接触; 与碳/ 碳复合材料的相容稳定性,既可防止涂层被碳还原而退化, 又可防止碳通过涂层向外扩散氧化; 具有低的挥发性, 避免高温下自行退化和防止在高速气流中很快被侵蚀。
硅基陶瓷具有最佳的热膨胀相容性, 在高温时具有最低的氧化速率, 比较硬且耐烧蚀。 SiC 具有以上优点并且原料易得, 当 02 分压较高时, 其氧化产物固态 SiO2 在 1650oC 以下是稳定的, 形成的玻璃态 SiO2 薄膜能防止 02进一步向内层扩散。 因此, 在碳/ 碳表面渗上一层 SiC 涂层, 能有效地防止碳/ 碳在高温使用时的氧化。 在碳/ 碳表面形成 SiC 涂层的方法有两种: 一种方法是采用固体扩散渗 SiC 工艺, 另一种方法是近年来采用的化学气相沉积法。 此外, 利用硅基陶瓷涂层(SiC、 Si3C4)对碳/ 碳进行氧化防护, 其使用温度一般在 1700~1800oC 以下, 高于 1800oC 使用的碳/ 碳复合材料的氧化防护问题还有待研究解决。
2)抑制剂法 从碳/ 碳复合材料内部抗氧化措施原理来说, 可以来取两种办法, 即内部涂层和添加抑制剂。 内部涂层是指在碳纤维上或在基体的孔隙内徐覆可起到阻挡氧扩散的阻挡层。 但由于单根碳纤维很细(直径约 7um), 要预先进行涂层很困难, 而给碳/ 碳复合材料基体孔隙内涂层, 在工艺上也是相当困难的。
因此,内部涂层的办法受到很大限制。 而在碳/ 碳复合材料内部添加抑制剂, 在工艺上相对容易得多, 而且抑制剂或可以在碳氧化时抑制氧化反应, 或可先与氧反应形成氧化物, 起到吸氧剂作用。 在碳、 石墨以及碳/ 碳复合材料中, 采用抑制剂主要是在较低温度范围内降低碳的氧化。 抑制剂是在碳/ 碳复合材料的碳或石墨基体中, 添加容易通过氧化而形成玻璃态的物质。 研究表明, 比较经济而且有效的抑制剂主要有 B203, 、 B4C 和 ZrB2 等硼及硼化物。 硼氧化后形成 B202; 具有较低的熔点和强度, 因而在碳和石墨氧化的温度下, 可以在多孔体系的碳/ 碳复合材料中很容易流动, 井填充到复合材料内连的孔隙中去, 起到内部涂层作用,既可阻断氧继续侵入的通道, 又可减少容易发生氧化反应的敏感部位的表面积。
同样, B4C、ZrD2 等也可在碳氧化时生成一部分 CO 后, 形成 B302, 例如 B4C 依以下反应形成 B203。 研究表明, 抑制剂在起到抗氧化保护时, 碳/ 碳复合材料有一部分已经被氧化。 硼酸盐类玻璃形成后, 具有较高的蒸气压以及较高的氧的扩散渗透率。因此, 一般碳/ 碳复合材料采用 内含抑制剂的方法, 大都应用在 600oC 以下的防氧化。更多碳碳复合材料信息可查看http://www.tqtf008.top
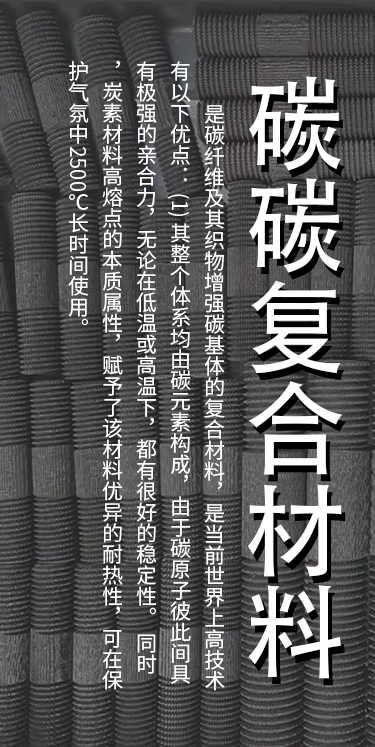
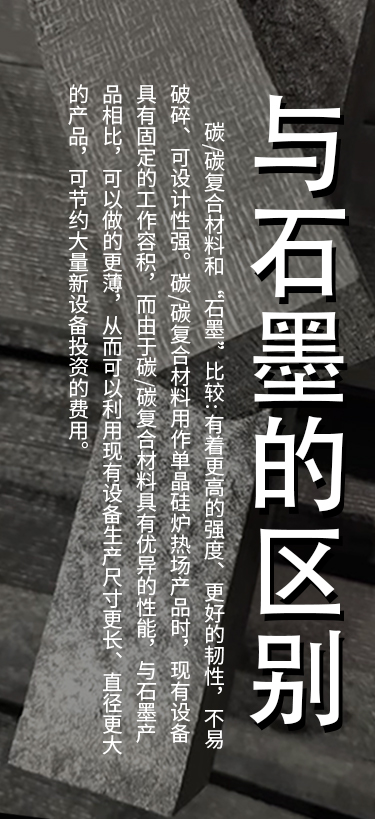